Welding wires, also known as filler wires, play a critical role in welding processes by ensuring strong, durable, and high-quality joints. They are essential in industries such as construction, automotive, shipbuilding, and manufacturing. Here’s an overview of the benefits and types of welding wires:
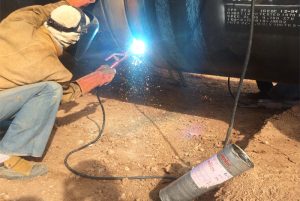
Advantages of Welding Wires
- High Efficiency: Welding wires allow for faster welding processes, increasing productivity in large-scale projects.
- Strong and Durable Joints: They create strong and reliable welds, ensuring structural integrity in demanding applications.
- Consistency: Automatic feeding of welding wires ensures uniform deposition, improving the quality of welds.
- Versatility: Suitable for a wide range of materials and welding techniques, such as MIG, TIG, and submerged arc welding.
- Cost-Effective: High deposition rates reduce waste, making welding wires more economical in long-term projects.
- Corrosion Resistance: Many types of welding wires provide corrosion resistance, extending the lifespan of welded components.
- Ease of Use: Welding wires simplify the welding process, especially in automated and semi-automated systems.
Types of Welding Wires
- Solid Welding Wire: Commonly used in MIG (Metal Inert Gas) welding, it is suitable for welding mild steel, stainless steel, and aluminum. It provides clean welds with minimal spatter.
- Flux-Cored Welding Wire: Ideal for outdoor applications, it eliminates the need for shielding gas and offers excellent penetration, even in dirty or rusty metals.
- Stainless Steel Wire: Designed for welding stainless steel, it offers corrosion resistance and is widely used in industries like food processing and chemical manufacturing.
- Aluminum Welding Wire: Lightweight and corrosion-resistant, it is used in applications like aerospace, automotive, and marine industries.
- Low Alloy Steel Wire: Perfect for welding high-strength steels, offering enhanced mechanical properties for demanding applications.
- Copper Coated Wire: Known for its conductivity and smooth feeding, it is primarily used in MIG welding for improved electrical performance.
- Nickel Alloy Wire: Suited for high-temperature and corrosive environments, such as power plants and petrochemical industries.
Why Choose the Right Welding Wire?
Selecting the appropriate welding wire ensures better weld quality, reduces repair costs, and improves overall project efficiency. Factors like base material, welding technique, and project requirements should be considered when choosing welding wires. At Nextera Commerce, we provide a wide range of premium welding wires to meet the needs of various industries. Whether you need flux-cored wires for outdoor projects or stainless steel wires for corrosion resistance, we have the right solution for you. For product catalogs, technical specifications, or additional information, please email us. Trust NexteraCommerce for high-quality welding wires that deliver exceptional performance every time.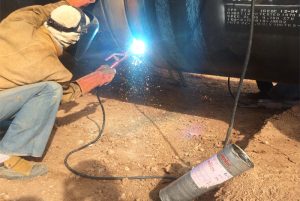